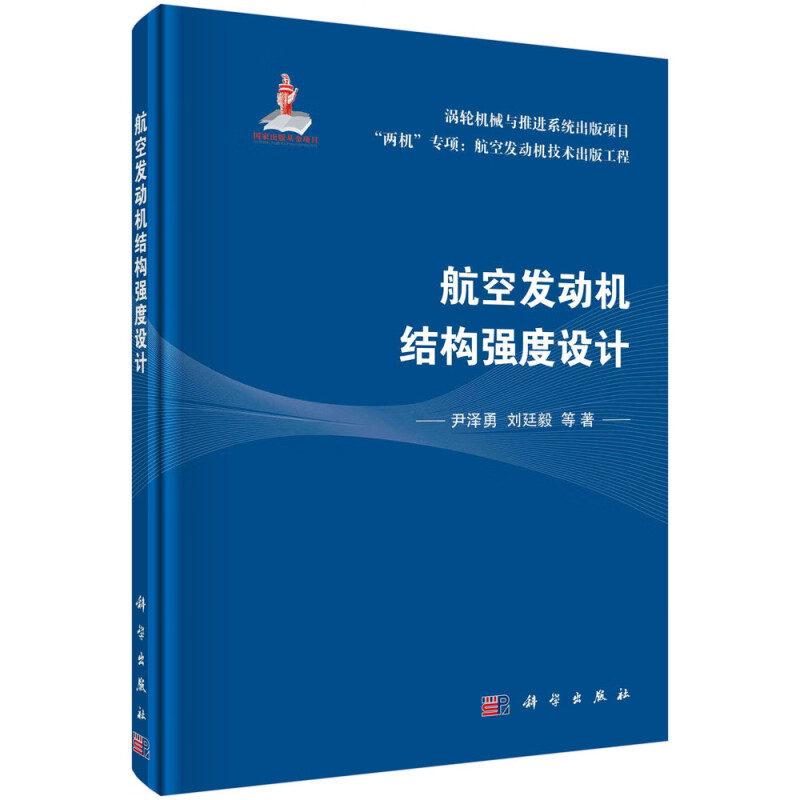
包邮航空发动机结构强度设计

- ISBN:9787030737229
- 装帧:一般胶版纸
- 册数:暂无
- 重量:暂无
- 开本:B5
- 页数:416
- 出版时间:2022-11-01
- 条形码:9787030737229 ; 978-7-03-073722-9
内容简介
本书航空发动机结构强度工程设计的角度,首先介绍航空发动机研制对结构强度的要求以及通用流程;然后分别从轮盘、叶片、主轴及转子连接件、机匣及其连接件、传动构件、转子动力学、整机振动及测试七个方面进行了介绍,每一部分主要包括该类构件在结构强度设计中经常遇到的失效模式、设计要求、流程及方法;*后总结航空发动机结构强度专业现今面临的挑战,提出未来发展趋势。
目录
涡轮机械与推进系统出版项目?序
“两机”专项: 航空发动机技术出版工程?序
前言
第1章绪论
1.1航空发动机结构强度设计的关联工作002
1.2航空发动机结构强度设计规范和准则003
1.3航空发动机结构强度设计方法的发展和进步004
1.4本书特点及内容安排006
第2章总体载荷
2.1概述007
2.2发动机整机载荷传递路径010
2.3发动机顶层载荷设计011
2.3.1发动机载荷设计流程011
2.3.2顶层载荷要求011
2.3.3发动机实际工作过程中的影响因素019
2.4发动机载荷设计方法019
2.4.1发动机气动载荷设计分析方法019
2.4.2发动机机动载荷设计分析方法022
2.4.3非正常载荷计算027
2.5发动机试车载荷谱设计及验证029
2.5.1整机耐久性试车分类029
2.5.2寿命试车载荷谱设计030
2.5.3高周疲劳专项试车载荷谱设计031
2.5.4转子气动轴向力测试031
第3章轮盘强度设计
3.1概述034
3.2轮盘结构特征035
3.2.1风扇盘的结构特征035
3.2.2压气机盘的结构特征037
3.2.3涡轮盘的结构特征038
3.3轮盘强度设计通用要求及准则039
3.3.1轮盘强度设计通用要求039
3.3.2轮盘强度设计准则041
3.4轮盘强度设计流程043
3.5轮盘载荷与环境045
3.6轮盘静强度设计047
3.6.1轮盘应力及变形计算方法047
3.6.2轮盘榫槽应力及变形计算方法054
3.6.3轮盘破裂特征及其破裂转速计算方法056
3.7轮盘寿命设计058
3.7.1轮盘低周疲劳寿命设计方法058
3.7.2轮盘蠕变及持久寿命设计方法063
3.7.3轮盘损伤容限设计方法067
3.8轮盘强度及寿命试验验证要求073
3.8.1轮盘强度及寿命试验测试的内容与要求073
3.8.2轮盘强度及寿命试验件设计081
3.8.3轮盘强度及寿命试验结果分析评定082
3.9轮盘结构强度设计输出085
第4章叶片强度设计
4.1概述087
4.2叶片结构特征088
4.2.1风扇/压气机叶片的结构特征088
4.2.2高/低压涡轮叶片的结构特征090
4.3叶片强度设计要求092
4.3.1叶片强度设计通用要求092
4.3.2叶片强度设计准则095
4.4叶片强度设计流程101
4.5叶片载荷与环境104
4.6叶片静强度设计105
4.6.1叶身静强度设计方法105
4.6.2叶片榫头静强度设计方法110
4.6.3叶冠静强度设计方法113
4.6.4叶片抗外物损伤设计方法115
4.6.5新结构、新材料叶片静强度设计方法119
4.7叶片振动与疲劳寿命设计123
4.7.1叶片振动特性设计方法123
4.7.2叶片高周疲劳设计方法127
4.7.3叶片颤振特性设计方法130
4.7.4叶片低周(热机械)疲劳寿命设计方法132
4.7.5叶片蠕变及持久寿命设计方法135
4.8叶片强度及寿命试验验证要求137
4.8.1叶片强度及寿命试验测试的内容及要求137
4.8.2叶片强度及寿命试验件设计141
4.8.3叶片强度及寿命试验结果分析评定146
4.9叶片结构强度设计输出147
第5章主轴强度设计
5.1概述149
5.2主轴及转子连接件结构特征150
5.2.1主轴结构特征150
5.2.2转子连接件结构特征150
5.3主轴强度设计通用要求及准则154
5.3.1主轴强度设计通用要求154
5.3.2主轴强度设计准则155
5.4主轴强度设计流程157
5.5主轴载荷与环境159
5.6主轴静强度及寿命设计160
5.6.1主轴静强度及寿命设计分析方法160
5.6.2转子连接结构强度及密封性设计分析方法179
5.7主轴振动设计192
5.7.1主轴振动特性192
5.7.2主轴振动设计分析方法192
5.7.3端齿连接结构振动特性及其建模方法198
5.8主轴强度及寿命试验验证要求199
5.8.1主轴强度及寿命试验测试的内容与要求200
5.8.2主轴强度及寿命试验设计202
5.8.3主轴强度及寿命试验结果分析评定203
5.9主轴强度设计输出204
第6章机匣强度设计
6.1概述206
6.2机匣及其连接件结构特征207
6.2.1进气机匣207
6.2.2风扇/压气机机匣208
6.2.3中介机匣210
6.2.4燃烧室机匣211
6.2.5涡轮机匣211
6.2.6涡轮后承力机匣214
6.2.7排气机匣215
6.2.8机匣连接结构217
6.2.9机匣新材料、新工艺与新结构218
6.3机匣强度设计通用要求及准则219
6.3.1机匣强度设计通用要求219
6.3.2机匣强度设计准则221
6.4机匣强度设计流程223
6.5机匣载荷与环境225
6.5.1气体作用力225
6.5.2温度载荷225
6.5.3质量惯性力226
6.5.4摔机载荷226
6.6机匣静强度与振动设计226
6.6.1机匣静强度及变形设计方法226
6.6.2叶片调节机构静强度及刚度设计方法236
6.6.3机匣连接件静强度及刚度设计方法238
6.6.4机匣振动设计方法242
6.6.5机匣包容性设计方法244
6.7机匣寿命设计250
6.7.1机匣低周疲劳寿命设计方法250
6.7.2机匣高周疲劳寿命设计方法254
6.7.3机匣蠕变/应力断裂寿命设计方法256
6.8机匣强度及寿命试验验证要求257
6.8.1机匣强度及寿命试验验证测试的内容与要求257
6.8.2机匣强度及寿命试验件设计260
6.8.3机匣强度及寿命试验结果分析评定260
6.9机匣结构强度设计输出262
第7章机械传动系统强度设计
7.1概述264
7.2机械传动系统结构特征266
7.2.1轴结构特征266
7.2.2齿轮结构特征267
7.2.3机匣结构特征270
7.3机械传动系统强度设计要求273
7.3.1轴的强度设计要求273
7.3.2齿轮的强度设计要求275
7.3.3机匣的强度设计要求277
7.4机械传动系统强度设计流程278
7.4.1轴的强度设计流程278
7.4.2齿轮的强度设计流程278
7.4.3机匣的强度设计流程279
7.5机械传动系统的载荷与环境284
7.5.1轴的载荷与环境284
7.5.2齿轮的载荷与环境284
7.5.3机匣的载荷与环境287
7.6机械传动系统静强度及寿命设计288
7.6.1轴的静强度及寿命设计方法288
7.6.2齿轮的静强度及寿命设计方法290
7.6.3机匣的静强度及寿命设计方法294
7.7机械传动系统振动设计297
7.7.1轴的振动设计方法297
7.7.2齿轮的振动设计方法306
7.7.3机匣的振动设计方法308
7.8机械传动系统试验验证要求313
7.8.1轴的试验验证要求313
7.8.2齿轮的试验验证要求314
7.8.3机匣的试验验证要求315
7.8.4附件传动系统、体内减速器、主减速器等的试验验证要求317
7.9机械传动系统结构强度设计输出317
7.9.1轴的强度设计输出317
7.9.2齿轮强度设计输出318
7.9.3机匣强度设计输出318
第8章转子结构动力学设计
8.1概述319
8.2转子支承结构特征320
8.2.1转子结构特征320
8.2.2承力结构特征323
8.3转子结构动力学设计通用要求及准则329
8.3.1转子结构动力学通用要求329
8.3.2转子结构动力学设计准则332
8.4转子结构动力学设计流程334
8.5转子运动及旋转惯性载荷336
8.5.1转子运动336
8.5.2旋转惯性载荷337
8.6转子系统模态特性设计341
8.6.1共振转速分布特性341
8.6.2双转子临界转速确定345
8.7转子系统振动响应特性设计350
8.7.1转子振动响应及支点动载荷350
8.7.2转静件碰摩激励转子振动响应356
8.8转子系统稳定性设计359
8.8.1弯曲刚度非对称及转子稳定性359
8.8.2转动惯量非对称及转子稳定性364
8.8.3转子结构内阻尼激励及稳定性368
8.9支承结构动力学特性设计376
8.9.1轴承激励特征设计376
8.9.2轴承支承刚度特性设计379
8.10转子结构动力学设计输出381
第9章未来航空发动机结构强度技术的研究方向及工作原则
9.1航空发动机结构强度工作的重要性383
9.2未来航空发动机结构强度技术的若干重要研究方向383
9.3未来航空发动机结构强度的工作原则387参考文献389
节选
第1章 绪论 航空发动机是航空飞行器的动力,对飞行器长时间高性能及安全可靠工作起着至关重要的作用。1903 年,世界上首次实现有动力飞行之后,活塞式航空发动机在20世纪40年代取得长足发展并使用至今,但主要是功率在几百千瓦以下的小发动机。20 世纪中叶以来,燃气涡轮喷气发动机得到迅猛发展及广泛应用,其压气机压比、涡轮前温度转子转速、推(功)重比、单位流量推力(功率)、 使用寿命及安全性可靠性等大幅提升,耗油率、噪声、污染排放及研发使用成本等显著降低,已成为当今航空发动机的主要形式。 无论是燃气涡轮发动机综合性能的大幅提升,以及近年来对环境友好燃气涡轮发动机提出的苛刻排放及高效率要求,还是今后新构型、新循环燃气涡轮发动机的综合性新目标的实现,都离不开航空发动机结构强度领域的科技进步。 这里所说的航空发动机“结构强度"是指:在航空发动机静态及动态高压气动载荷、高速旋转件离心力及陀螺力等机械载荷;在高温热载荷等作用下,航空发动机的盘、轴、叶片、机匣等各类构件的刚度(即变形状况)、静强度及抗冲击能力;这些构件的振动强度、高周疲劳寿命、低周疲劳寿命、蠕变寿命及持久寿命;航空发动机的转子动力学特性和整机振动特性等。 航空发动机结构强度工作内容很多,主要包括:结构设计,即确定构型及构件的形状尺寸、选择构件材料、制定构件制造工艺;结构强度设计,即结构强度要求、结构强度分析、结构强度试验等。本书以强度设计方面的内容为主,以结构、材料、工艺方面的内容为辅,其中强度设计方面又以结构强度设计的计算分析方法为主,要求、流程、载荷等为辅,对强度试验仅关注其验证要求。 本章简要介绍航空发动机结构强度设计工作所涉及的学科及领域、应遵从的规范及准则,以及结构强度设计方法的发展和进步等,*后说明本书的特点及内容安排。 1.1 航空发动机结构强度设计的关联工作 航空发动机结构强度设计工作当然与发动机的结构设计密不可分。航空燃气涡轮发动机主要有四种基本类型,即涡轮喷气发动机、涡轮风扇发动机、涡轮螺桨发动机和涡轮轴发动机,均包括压气机、燃烧室(部分还有加力燃烧室)、涡轮、尾喷管等主要部件及一些系统。当然,这些部件又有不同形式,如压气机及涡轮有轴流式、离心式(向心式)或组合式,燃烧室有直流式及回流式等。各类压气机转子或其分段转子均由涡轮转子或对应的分段转子带动旋转,涡扇发动机中特有的风扇转子及飞机或直升机的螺旋桨、旋翼也由相应的涡轮转子带动旋转。 无论是哪一类型的航空发动机,是大推力/功率还是小推力/功率航空发动机,其基本构型及各类构件形状可以说是大致相同的。从其刚度、强度、振动、寿命、转子动力学特性及整机振动特性等所涉及的固体力学、机械振动学、气动力学、传热学、计算力学等学科视角来看,航空发动机结构强度设计工作的对象不外乎是高速旋转的轴、盘、叶片及其所形成的转子及转子系统,通过支板、轴承座来支承转子并传递各种载荷的内、外机匣及安装在机匣上的静子叶片等形成的静子及静子系统,后者又通过外机匣与飞行器机体或短舱机械连接。虽然各类发动机的刚度、强度、振动、寿命、转子动力学特性及整机振动特性等的结构强度设计方法没有本质性区别,然而在使用环境和使用方法有异的航空发动机之间,或同一航空发动机的不同结构设计方案之间,各构件的具体受力状况大不相同,因此其结构强度设计的结果肯定不一样,甚至差别很大。在满足使用要求及有关结构限制条件下,努力寻求结构强度*好的构型布局及构件形状尺寸,正是在航空发动机研制过程中反复开展的结构强度设计工作的重要任务。 航空发动机的刚度强度、振动、寿命转子动力学特性及整机振动特性等结构强度设计工作,除与其结构设计密切相关外,也与其构件选用材料密切相关。台航空发动机由成千上万个零件组成,每类零件又采用不同的材料。目前,制造航空发动机构件的金属材料主要有结构钢、不锈钢、高温合金、钛合金、铝合金、镁合金等,非金属材料主要有橡胶、石墨、复合材料、涂层涂料等。发动机的压气机等冷端部件常选用钛合金、结构钢和不锈钢,热端部件多采用变形高温合金、铸造高温合金和粉末高温合金,随着树脂基、金属基及陶瓷基复合材料的制造成熟度逐渐提高,也得到了许多应用。随着航空发动机技术的快速发展,对高比强度、高比刚度、耐腐蚀材料及耐更高温度材料的需求越来越强烈,各类新型材料仍在不断发展和应用。材料性能包括密度弹性模量、导热系数等基本物理参数,弹性极限、屈服极限、强度极限等强度参数,以及断裂、蠕变、持久特性等寿命参数。对于这些性能参数的了解与把握不足,就不可能在航空发动机结构强度设计工作中正确选择材料,也不可能获得*好的刚度、强度、振动、寿命、转子动力学特性及整机振动特性。 此外,航空发动机结构强度设计工作也与其制造工作密切相关。每一个构件都要分别或联合采用质量高、经济性好的铸造、锻造、切削加工、增材制造等冷热工艺生产,以全面符合设计要求,其中包括对构件刚度、强度振动、寿命、转子动力学特性及整机振动特性的要求。显而易见,发动机制造过程中,所有的制造工艺都要稳定可控,并努力提高被加工零部件的力学性能水平。在航空发动机结构强度设计工作开展之前,虽然已按严格规定的试样状态、形状、尺寸及测试方法获取了大量精确力学性能数据,并纳人航空发动机材料性能数据手册及数据库中供结构强度设计使用,但很多时候还需要选取已制造零件的不同部位再次取样,补充测试其力学性能数据,以考虑不同制造工艺对构件力学性能的具体影响,从而保证构件的刚度、强度、振动、寿命、转子动力学特性及整机振动特性等结构强度设计结果更加准确。 由于篇幅有限,本书对于与航空发动机结构强度设计工作密切相关的结构设计、材料选择及工艺制定虽有涉及但介绍不够详细,请读者在实际工作中多加注意。另外,从学科领域来看,发动机结构强度设计工作除了与固体力学直接相关外,还与气动力学、热力学、燃烧学、计算力学等密切相关,书中未能详细叙述,读者必要时可参考相关资料。 1.2 航空发动机结构强度设计规范和准则 航空发动机行业早期,过分重视航空发动机气动热力性能而忽略了结构强度问题。经过多年的惨痛教训、艰苦探索与细致研究,在解决新机研制及旧机使用中不断出现的航空发动机各类结构强度故障的过程中,航空发动机的研制原则发生了根本性改变。 从20世纪60~70年代开始,逐步形成了航空发动机的气动热力性能与其结构完整性、可靠性及维修性等并重,提高产品综合效能的研制指导思想,据此形成的航空发动机通用规范与结构强度设计准则等是航空发动机产品研制和批量生产的重要指导性文件,是航空发动机结构完整性、可靠性等技术要求的有力保障。20世纪50年代,美国基于涡喷涡扇和涡轴涡桨发动机研制、使用过程中积累的经验,编制了《航空发动机通用规范》(MIL-E-5007A)和《涡轮轴和涡轮螺桨发动机通用规范》(MIL-E-8593A),规定了对航空发动机结构、性能、环境、完整性、可靠性/维修性、生存力等的要求,其中许多篇幅直接或间接与结构强度设计工作有关。 后来,研究人员根据航空发动机研发和使用实践对其进行了多次修订,并将MIL-E-5007A和MIL-E-8593A进行融合,发布了《航空涡喷涡扇涡轴涡桨发动机通用规范》(JSGS- 87231A)等- -系列规范。英国于20世纪60年代颁布的通用规范也几经修订,英国国防部于21世纪初发布了新版DEF STAN 00-970: 11。同样,我国也于20世纪80年代分别颁布了《航空涡轮喷气和涡轮风扇发动机通用规范》(GJB241-1987)和《航空涡轮螺桨和涡轮轴发动机通用规范》(CJB242-1987),并在21世纪初作了修订,根据规范中的结构完整性和可靠性等要求,直接或间接地指导开展航空发动机结构强度设计工作。此外,国内外适航规章的相关部分也具备这种指导作用。 更具体地,随着航空发动机刚度强度、振动、寿命、转子动力学特性及整机振动特性等工作的不断深入开展,美国于1984年以军用标准的形式颁布了第1版《发动机结构完整性大纲》( ENSIP MIL- STD- 1783),并于2002年修订并颁布了第3版《发动机结构完整性大纲》( ENSIP MIL- HDBK - 1783B)。英国罗尔斯.罗伊斯公司(简称罗.罗公司)根据多年研制经验,很早就针对斯贝MK 202发动机制定了《斯贝MK 202发动机应力标准( EGD- 3)》,其结构强度设计准则、评定标准和分析方法对当时的航空发动机结构强度设计工作具有具体指导作用。据悉,俄罗斯中央航空发动机研究院多年前就制定了自己的航空发动机结构强度设计准则,美欧相关企业同样有自已的结构强度设计准则。 我国的航空发动机研发单位也早在多年前就编写出版了《航空发动机强度设计、试验手册》,之后,陆续以国军标的形式颁布了《航空发动机结构完整性指南》(GJB/Z101-1997),并组织编写了《航空涡喷、涡扇发动机结构设计准则(研究报告)》包含发动机结构强度、振动、寿命、转子动力学特性及整机振动特性等内容的《航空发动机设计手册》及《航空燃气涡轮发动机结构强度设计》等。 必须指出,航空发动机结构强度设计工作遵从发动机规范及结构强度设计准则开展,航空发动机结构强度设计准则是对满足规范中相关原则要求的具体量化规定,是对发动机研制、使用过程中所开展的结构强度设计工作丰富经验的不断总结提炼,是一个国家或公司技 术竞争力的重要体现,具体内容并未公开。 1.3 航空发动机结构强度设计方法的发展和进步 随着航空发动机技术的不断发展进步,航空发动机结构强度设计方法不断发展进步并与其他学科融合。20世纪40~ 50年代,在航空发动机结构强度设计工作中只需设计满足*低安全系数要求的静强度并避开共振区,将构件简化为采用材料力学方法或其他解析方法就可以处理的轴、盘梁、筒,计算工具是计算尺或手摇计算机。20世纪50~60年代,对航空发动机寿命有了明确要求,在结构强度设计工作中逐步发展建立了持久、蠕变和高、低周疲劳的寿命分析模型,开展了安全寿命结构强度设计工作。 随着电子计算机技术及计算力学的快速发展,基于弹塑性理论、断裂力学及先进机械振动理论等的有限元法及其他数值分析方法开始在航空发动机结构强度设计工作中发挥越来越重要的作用。20世纪70年代前后,采用有限元分析方法对构件进行简化,然后针对二维平面应力或平面应变问题、轴对称问题或板壳问题等进行分析。经过50多年的发展,随着计算速度的不断提高及计算规模的日益扩大,有限元的基础理论和分析方法已经相当成熟,已有能力完全采用连续介质力学方法甚至微观宏观耦合方法来处理航空发动机的结构强度设计问题。 目前,大型商用有限元分析软件及各类专用软件基本具备了包括航空发动机所有零部件的一/二/三维刚度、强度振动、寿命、转子动力学特性及整机振动特性分析等功能。此外,借助分析能力十分强大的有限元分析软件,人们不仅可以对单个构件及存在应力集中的细节部位专门展开精细分析,还可将分析范围扩大到部件乃至整机,以避免边界条件模拟不准确造成的对感兴趣部位或构件受力状况的影响。如有必要,甚至还可模拟航空发动机结构从制造、装配到使用全过程的受载及力学状况变化历程,从而获得十分准确的时变应力、应变场。当然,也可以模拟从零部件到转、静子系统乃至整机的抗冲击状况及各类振动状况随时间的变化过程。 其实,上面所述方法的准确性不同,计算分析工作量各异,但在航空发动机研制的方案设计、初步(技术)设计、详细设计三个不同设计阶段中,以及在研制、使用中排除结构强度故障时,都可发挥各自特有的作用。-.般原则是在设计初期采用准确性不太高但工作量较小的方法,在设计中、后期及排故分析时,则采用准确性更高但工作量也更大的结构强度设计方法。
-
黑科技驱动世界的100项技术
¥21.9¥69.8 -
中国传统民俗文化:建筑系列:中国古代桥梁
¥19.6¥58.0 -
黑科技:驱动世界的100项技术(八品)
¥21.9¥69.8 -
工业机器人操作与编程
¥19.6¥58.0 -
新能源汽车构造原理与仿真技术研究
¥20.1¥59.8 -
服装生产讲座③(修订版)立体裁剪 基础编
¥35.8¥58.0 -
大家小书:世界桥梁趣谈
¥13.9¥35.0 -
城镇市容环境卫生建设标准汇编 垃圾分类、检测和收集转运卷
¥153.0¥180.0 -
磷酸铁锂动力电池故障机理及诊断方法研究
¥17.7¥49.0 -
环卫与环保机械/工程机械手册
¥174.9¥318.0 -
陈总编爱车热线书系汽车不神秘:汽车构造透视图典(全彩典雅版)
¥52.0¥69.9 -
大数据时代石油价格的复杂性及预测
¥29.3¥42.0 -
渡河工程
¥20.2¥60.0 -
机械振动基础
¥21.3¥35.0 -
现代制造技术
¥30.0¥43.0 -
石油数据组织与分析
¥28.0¥40.0 -
图说胶济铁路故事:下
¥20.0¥50.0 -
儿童玩具安全物理危害风险评估方法及应用基于使用场景不确定性
¥25.4¥28.0 -
图说胶济铁路故事(中)
¥20.0¥50.0 -
津沽铁路的历史记忆
¥17.2¥40.0